By: PFI
May2024
Digitalization and sustainability, the two primary focuses of MetaSkill4TCLF, are not merely coincidental megatrends in our century. Instead, they are intricately intertwined. As the world becomes increasingly digital, it unlocks new opportunities and features through advancements in digitization. However, while digitalization can be a powerful tool for sustainability management, it also carries a darker side. This is evident in the sharp rise of electronic waste. In 2022 alone, a staggering 62 million tons of e-waste were produced, marking an 82% increase from 2010. Projections suggest this figure could further escalate by 32%, reaching 82 million tons by 2030. Despite these concerning statistics, only a fraction (22.3%) of the year's e-waste mass was properly collected and recycled in 2022, leaving an estimated $62 billion worth of recoverable natural resources unaccounted for and increasing pollution risks worldwide (1).
Responsible waste management is crucial to prevent ourselves from drowning in our own waste. To achieve this, disposal considerations must be integrated into the very design phase of products. This entails ensuring that electronic components are reversibly integrated into products, facilitating separate disposal processes.
The integration of electronics into shoes and textiles presents a multitude of possibilities, seamlessly blending functionality with innovation. Embedded sensors and electronics can monitor movement, track health metrics, or offer feedback on posture and balance. GPS tracking capabilities can aid in locating vulnerable individuals, such as children and the elderly, while LED lights enhance both aesthetics and safety in low-light conditions. Additionally, features like heating and cooling elements provide comfort in extreme weather conditions. These examples underscore the vast potential of smart shoes and clothing to enhance everyday experiences and improve overall well-being.
When developing products with electronic components, the focus of the design is often on functionality and costs rather than sustainability. However, if the electronic components cannot be easily detached from the rest of the product, the product as a whole counts as electronic waste, creating a predicament from both sustainability and waste disposal perspectives. In the EU the Waste Electrical and Electronic Equipment Directive (3) regulates the disposal of electronic devices, in Germany the directive is implemented through the Electrical and Electronic Equipment Act (ElektroG) (4). Manufacturers must register products with the Elektro-Altgeräte Register (Waste electrical equipment register) and responsibly recycle an equivalent amount of electronic mass as they have sold. Therefore, whether the whole product or just the reversible integrated electronics (circuit board/battery) requires disposal as electrical waste becomes a crucial aspect not only from the aspect of sustainability but also from an economic point of view.
Finding ways to seamlessly incorporate various electronic components into footwear, ensuring they can be easily removed if needed, while maintaining functionality, safety, and durability, may pose a significant challenge. Possible solutions for these challenges are currently being investigated at the PFI - Prüf- und Forschungsinstitut Pirmasens e.V. (Test and Research Institute Pirmasens) and the University of Applied Sciences Kaiserslautern (Faculty Computer Science and Microsystems Engineering) in a project funded by the Federal Ministry for Economic Affairs and Climate Action (2).
The project aims to create three demonstrators with diverse electronic functionalities, all of which share the common aspect of seamlessly and reversibly integrating electronics into shoes. One concept centers around gait analysis, and the measure of temperature and humidity (“health shoe”), while the two other demonstrators draw inspiration from established applications like "heated shoes" and "flashing shoes” Safety as well as the continuous function of the shoes electronic feature is a central focus across all three integration concepts. Footwear is constantly and repetitively exposed to high loads therefore it is important to consider the safety and durability of the integrated electronics. Also, it needs to be taken into consideration that different features require different amounts of energy. For instance, the heated shoe necessitates a stronger LiPo battery due to its high energy demand. If a LiPo battery is mechanically loaded and contact between lithium and oxygen occurs, this can have serious consequences for the user. To mitigate this, it is advisable to situate the battery externally to the shoe. In contrast, flashing shoe mostly employs button cells to fulfill its energy requirements, given its low power consumption, smaller and more easily integrated into the sole. Despite different requirements and considerations for the different features the goal is a modular approach of the different concepts allowing an easy adaptation to new and extended features.
Therefore all 3 concepts are based on one common circuit board design containing a suitable microcontroller, inertial measurement unit (IMU), Gyroscope, current sensor, voltage converter (3.5V to 16V @ 250mA), LEDs and a radio module for information transfer.
The approach taken for the “health shoe” was relatively traditional, incorporating newly developed temperature and humidity modules into an insole. Gait data were provided by the IMU/Gyroscope on the circuit board. The circuit board with an incorporated charging unit and accompanied by a rechargeable pouch lithium battery (3.7 V, 140mAh), is enclosed within a casing and shielded by a carbon fiber plate. This casing is attached to the insole and designed to fit into a designated cavity located in the heel area. At the end of the lifespan of the shoe and/or the functional insole, the insole along with the embedded sensors and electronics, including the casing, can easily be removed, and discarded as electronic waste. Equipped with a dummy for the cavity and a normal insole, the shoe can also be worn without its functional health application.
The "flashing shoe" uses PMMA plastic fiber optics to replace the electronic components like cable and LEDs in the upper. The LEDs are located on the circuit board and only the light gets transferred to the location of the flashing design feature on the upper. At the end of the lifespan the fiber optics can remain in the shoe and the circuit board including the batteries can be removed from a heel cavity and disposed of separately. The "flashing shoe" employs the same circuit board as the “health shoe”, offering the potential for expanding its functionality. Flashing is activated in response to the signals from the Inertial Measurement Unit (IMU). Given that the shoe solely performs flashing and does not transmit any data, power demands are low. Two button cell batteries are therefore sufficient. If higher power consumption becomes necessary, the power concept of the health shoe can be employed. The circuit board presently houses two LEDs and slots into a casing in the heel cavity in a way that allows the LEDs to snuggly fit against the end of fiber optics, a crucial aspect to prevent light loss and maintain brightness where the fiber optic emerges from the upper for the desired flashing feature. The selection of fiber optics can depend on factors such as flexibility, diameter size, and the choice between "end glow" or "end and side glow". Incorporating the fiber optics during the production process and preventing fiber optic breaks requires some adaptation of the process. Although PMMA is a thermoplastic and can withstand heat effectively, its contact with acetone-based glue, for instance, can have adverse effects and elevate the risk of breakage. In addition, it is important to avoid sharp corners along the course of the fiber optics, a consideration that should be factored in during the design of the light feature optics.
The design of the "heated shoe" was based on the desire to use only materials that are commonly used in the shoe and textile industry, such as press studs or conductive yarn, to transmit the electrical current and produce the heat within the shoe. The circuit board (with a high current output regulator instead of a charging unit) and high-capacity LiPo batteries can be affixed to either the back or side of the shoe, allowing for easy removal in the unlikely event of a battery fire. The shoe and electronics are distinct entities, linked only by press studs and an extra securing mechanism like a loop or a plug in. However, it shall be noted that even though the circuit board and batteries can be easily separated, the remaining shoe is still classified as electronic waste under the German Waste Electrical Equipment Register. This is because the electricity that flowed through the conductive yarn and the press studs, was essential to fulfill the function of the product. Consequently, the yarn and studs would need to be removed for the rest of the shoe to be disposed of as non-electronic waste according to the wording of the law. This example underscores how legal frameworks and logical reasoning may sometimes diverge when seeking practical solutions for functional waste management.
The integration of electronics into shoes presents a complex array of challenges, including ensuring durability, comfort, user safety, privacy, data security, sustainability, and effective waste management. However, the potential to revolutionize daily life aspects, encompassing everything from health monitoring to immersive augmented reality experiences, makes smart footwear a pursuit rich with promise for both consumers and industries.
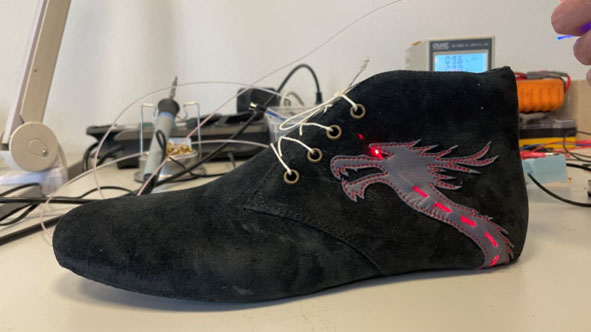
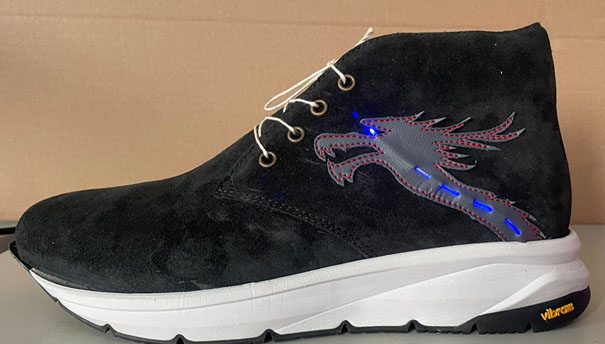
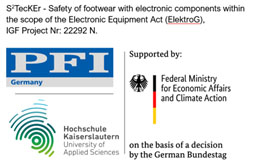
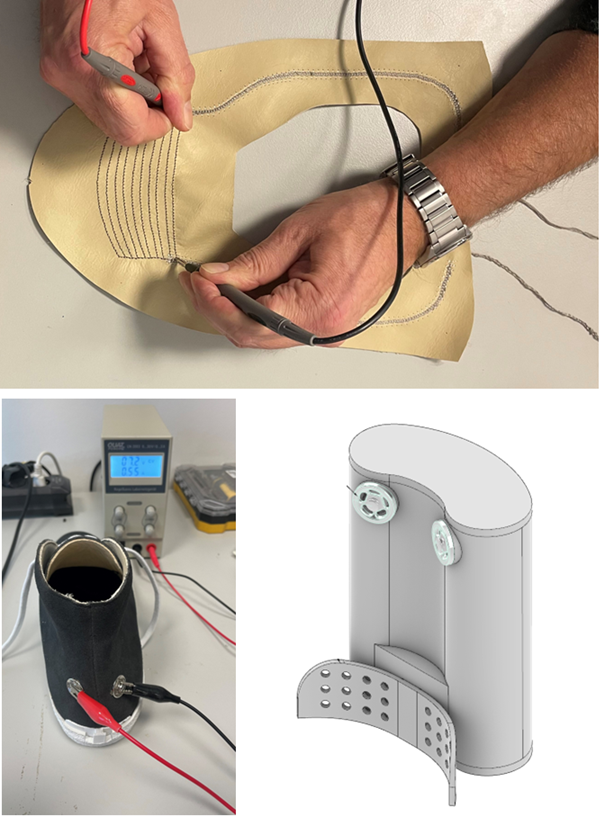
(1) Cornelis P. Baldé, et al. (2024). International Telecommunication Union (ITU) and United Nations Institute for Training and Research (UNITAR). 2024. Global E-waste Monitor 2024. Geneva/Bonn.
(2) Sicherheit von Schuhen mit elektronischen Komponenten im Rahmen des Elektronikgerätegesetzes – „S²tecKEr“, IGF Vorhaben-Nr. 22292 N.
(3) Directive 2012/19/EU on waste electrical and electronic equipment - WEEE-Directive
(4) Gesetz über das Inverkehrbringen, die Rücknahme und die umweltverträgliche Entsorgung von Elektro- und Elektronikgeräten – ElektroG 3
Author: PFI